Consommation d'Énergie dans le Moulage Sous Pression
Le moulage sous pression consiste à forcer du métal en fusion sous haute pression dans des moules en acier réutilisables. Bien que ce processus soit très efficace pour la production de masse, il est également très énergivore, notamment dans les étapes suivantes :
- Fours de fusion et de maintien : Ils consomment jusqu'à 60-70% de l'énergie totale dans une opération de moulage sous pression.
- Systèmes hydrauliques : Utilisés pour faire fonctionner les machines et les éjecteurs.
- Systèmes d'air comprimé : Utilisés dans l'automatisation, les systèmes de pulvérisation et de refroidissement.
- Systèmes de chauffage et de refroidissement des moules : Maintiennent la température du moule pour une qualité optimale du moulage.
- Opérations après moulage : Découpe, usinage et finition de surface.
Pour comprendre les enjeux réglementaires liés à l'efficacité énergétique industrielle, consultez les directives de l'ADEME (Agence de l'Environnement et de la Maîtrise de l'Énergie).
Stratégies Clés pour Améliorer l'Efficacité Énergétique
Mettre à Niveau vers des Fours de Fusion Haute Efficacité
Passez à des fours de fusion haute efficacité pour réduire la consommation d'énergie lors de la phase la plus énergivore du traitement du métal. Le choix de systèmes modernes tels que des fours à induction électrique pour les métaux non ferreux, des fours à gaz régénératifs ou des fours de fusion à tour peut entraîner des économies d'énergie substantielles.
Ces fours avancés sont conçus avec une isolation supérieure, offrent des temps de fusion plus rapides et permettent un meilleur contrôle de la consommation d'énergie. Si le volume de votre production le permet, envisagez de passer à la fusion par lots pour minimiser le gaspillage d'énergie pendant les périodes d'inactivité.
Implémenter un Suivi de l'Énergie en Temps Réel
L'installation de systèmes de gestion de l'énergie (SGE) permet de suivre de manière exhaustive la consommation d'énergie dans toutes les opérations, d'identifier les zones de forte consommation et de comparer l'utilisation de l'énergie par unité produite.
Avec des données en temps réel à portée de main, vous obtenez des informations précieuses qui peuvent être utilisées pour ajuster les processus, minimiser les déchets et garantir que vos opérations fonctionnent toujours à une efficacité maximale. Au fil du temps, le SGE aide à établir des objectifs d'économies d'énergie clairs et soutient la conformité aux normes de durabilité.
Optimiser la Gestion de la Température des Moules
Une régulation thermique efficace des moules joue un rôle vital dans la réduction du temps de cycle et l'amélioration de la qualité du moulage. La mise en place de couvertures isolantes pour les moules, de systèmes de chauffage de moules haute efficacité et de systèmes de refroidissement à eau en boucle fermée peut améliorer considérablement la gestion thermique.
Ces solutions travaillent ensemble pour minimiser la perte d'énergie tout en maintenant une température stable du moule, garantissant que le chauffage et le refroidissement ne sont pas utilisés de manière excessive et que la consommation d'énergie reste sous contrôle.
Récupérer et Réutiliser la Chaleur Perdue
Investir dans des systèmes de récupération de chaleur, tels que des récupérateurs et des échangeurs de chaleur, vous permet de capturer et de réutiliser la chaleur précieuse provenant des gaz d'échappement émis par les fours et les surfaces chaudes dans l'environnement de moulage.
Cette chaleur récupérée peut ensuite être redirigée pour préchauffer l'air de combustion, réchauffer l'eau d'alimentation ou contribuer au chauffage des espaces de l'usine. En utilisant efficacement la chaleur perdue, la consommation d'énergie globale est réduite et l'efficacité opérationnelle est considérablement améliorée.
Utiliser des Machines de Moulage Sous Pression Haute Vitesse et à Faible Consommation
Les machines modernes de moulage sous pression équipées de systèmes servo-hydrauliques apportent plusieurs avantages en matière d'économies d'énergie, tels que le contrôle de la vitesse variable, la réduction de la hausse de la température de l'huile et une consommation d'énergie réduite en mode veille.
Leur précision améliorée améliore non seulement la qualité du produit, mais réduit également les taux de rebut et le besoin de retouche, ce qui contribue indirectement aux économies d'énergie globales. Pour plus d'informations sur les technologies de pointe en métallurgie, consultez le CETIM (Centre Technique des Industries Mécaniques).
Automatiser Intelligemment
L'automatisation ne conduit pas nécessairement à une augmentation de la consommation d'énergie ; en fait, lorsqu'elle est conçue dans une optique d'efficacité, elle peut réduire considérablement les déchets et améliorer la performance globale.
Les systèmes d'automatisation écoénergétiques aident à maintenir des temps de cycle constants, minimisent les erreurs humaines qui entraînent souvent des pertes de matériaux et d'énergie, et permettent une planification intelligente et une gestion des charges. En intégrant des capteurs, de la robotique et des outils de planification basés sur l'IA, les fabricants peuvent optimiser l'utilisation de l'énergie dans toute la ligne de production.
Réduire les Rebuts et les Reprises
Chaque pièce défectueuse signifie une énergie gaspillée. Pour minimiser les rebuts :
- ✅ Utilisez des logiciels de simulation pour la conception des moules et des processus
- ✅ Appliquez la maintenance prédictive pour maintenir les machines en fonctionnement efficace
- ✅ Formez régulièrement le personnel aux normes de qualité
Réduire les reprises permet non seulement d'économiser de l'énergie, mais aussi de réduire les coûts des matériaux et d'améliorer la satisfaction des clients.
Passer aux Sources d'Énergie Renouvelables
Bien que l'optimisation des systèmes internes soit essentielle, la transition vers l'énergie solaire, éolienne ou verte réduit encore davantage votre empreinte carbone. De nombreuses installations de moulage sous pression installent des panneaux solaires sur les toits ou concluent des accords d'achat d'énergie verte pour alimenter leurs opérations.
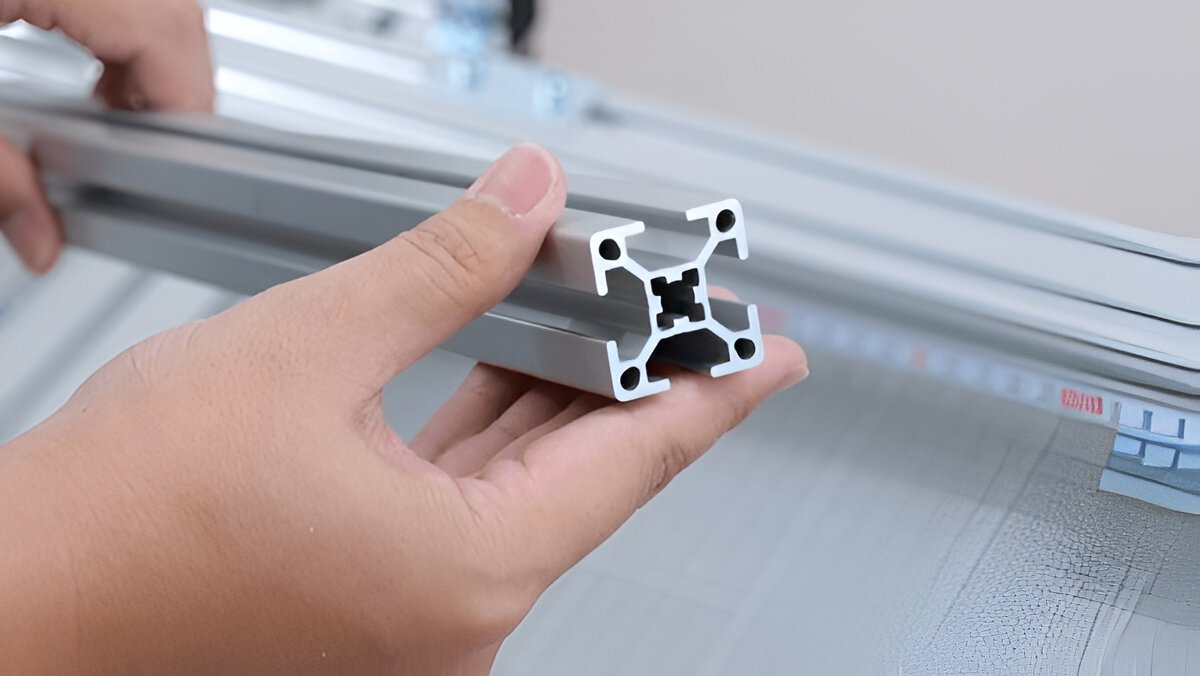
Avantages du Moulage Sous Pression Écoénergétique
La mise en œuvre de stratégies énergétiques efficaces dans les opérations de moulage sous pression conduit à :
🎯 Avantage | 📈 Impact |
---|---|
Coûts opérationnels réduits | Factures d'énergie réduites, surtout dans la fusion |
Compétitivité accrue | Coût de production par pièce réduit |
Meilleure qualité du produit | Températures constantes, moins de défauts |
Conformité réglementaire | Respect des normes d'émissions et d'énergie |
Meilleure image de marque | Alignement avec les objectifs de durabilité |